Foam can be a great cost-effective protective solution for your product. And there are a variety of ways it can be created, which are good to know when it comes to choosing the right type for your product. The method chosen all depends on the foam design, foam type, and quantity needed.
Here’s a quick rundown of five common foam fabrication methods:
Foam Fabrication Method #1: Die-Cutting
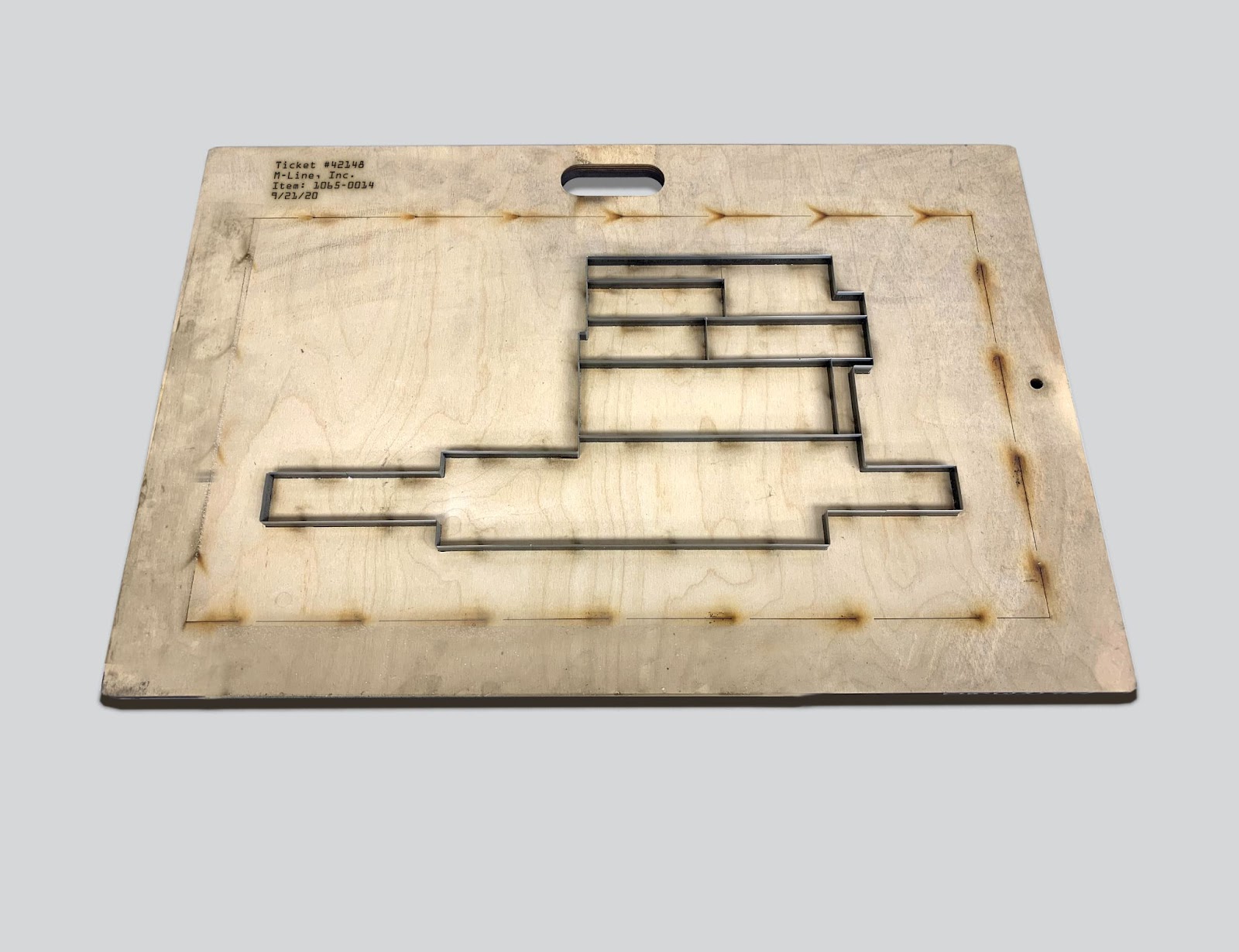
This method uses a steel rule die to stamp out the parts. It's a cost-effective, quick method of producing parts.
However, it may have some downsides. The initial tooling cost can be high, and concavity (an hourglass shape instead of a straight cut) can occur due to the foam compressing during the die-cutting process
Foam Fabrication Method #2: CAD Table Cutting

The foam plank is vacuumed onto a cutting table, and then various blades can be used to cut out shapes within the foam plank. The cutouts are all programmed into the machine via an engineering file.
There’s no tooling cost with this method, and no risk of concavity. However, it can be a slower process because of the speed limitations of the CAD table.
Download our guide to the four most common types of foam and see which one could be right for your product >>
Foam Fabrication Method #3: CNC Wire Cutting

A large foam bun is placed on a table, and a wire is run through the entire bun either horizontally or vertically.
CNC cutting can produce a large volume of foam at one time, and again, there’s no tooling cost. If there are any cutouts in the middle of a cavity or shape, there will need to be an entry point to create the cutout.
Foam Fabrication Method #4: Water Jet Cutting

Water under very high pressure is used to cut shapes out of the foam. Again, there’s no tooling cost and no concavity.
Water jet cutting can produce very small, precise shapes and letters - even nonstandard shapes with a 5-axis head. The parts do need drying time after being exposed to the water jet.
Foam Fabrication Method #5: Molding

With this method, foam is molded under heat and pressure using aluminum molds. It makes for inexpensive part costs, but because the molds themselves are very expensive, volumes of 10,000+ pieces are needed to make this a worthwhile option.
Foam Packaging From M-Line
M-Line can help with your foam needs - even (and especially) those that are out of the ordinary. Our sales and engineering staff can help you with every piece of the foam design as well as the best method to produce it.